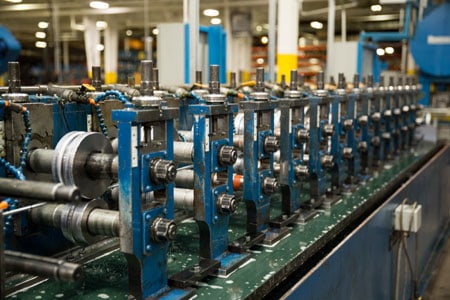
Roll forming—also stylized as roll-forming or roll forming—is a metalworking process that employs a series of rolls to continuously bend a coil of sheet metal until it has the desired profile. The rolls come in sets that are mounted on consecutive stands to facilitate the forming operation. As the strip—typically made of coiled steel—runs through the sets of rolls, each set incrementally produces a bend in the material.
At Premier Products of Racine, we are a full-service custom roll forming company. Equipped with two decades of experience and an over 210,000 square foot manufacturing facility, our expert team has the skills and equipment necessary to provide quality roll formed products at competitive prices.
The Roll Forming Process
Rolling forming operations use roll forming machines to bend coils of metal. The machines contain fixed rollers that guide the metal strips through and make the necessary alterations, bending the materials a little more at each subsequent set of rolls. This method of progressively bending the metal ensures the desired cross-sectional configuration is reached. Roll forming machines usually work at speeds of 30 to 100 feet per minute. The machine never stops during production so incredible quantities/hour of parts can be achieved.
The roll forming process offers a number of manufacturing benefits, including faster production speeds, greater production consistency and repeatability, and broader part versatility. It is suitable for large production runs of parts with uniform cross-sections.
Benefits of Roll Forming
Compared to other metalworking processes, roll forming offers several manufacturing benefits, including:
- Greater production efficiency. As the material used in roll forming operation is in coil form, the process proceeds at much higher speeds and requires lower manual involvement. These capabilities allow for faster production of larger volumes.
- Lower production costs. Other cost savings come from the process’s greater material utilization (reducing material waste and overall cost), incredible energy efficiency in the forming process superior surface finishes (eliminating the need for further machining or finishing), produce complex parts and shapes at speeds of 30-100 feet per minute and lower tool wear (decreasing the cost of tooling replacement over time).
- Better part design flexibility. The roll forming process easily produces complex profiles that are difficult to achieve through alternative manufacturing methods (e.g., stamping, bending), such as round, closed, and C-shape forms. Additionally, while other processes (such as extrusion) are limited to aluminum or brass, roll forming is suitable for virtually any metal, ferrous or nonferrous.
- Superior precision, quality, and consistency. Compared to press braking, roll forming can meet tighter tolerances while creating parts and products that are more consistent and uniform across multiple runs. Compared to extrusion, the process produces higher quality products.
Benefits of a Proprietary Cosmetic Roll Forming Process
At Premier Products of Racine, we designed our proprietary roll forming process to optimize production operations for difficult-to-roll form and highly cosmetic parts. The process increases production line speeds above industry standards, allowing for even better efficiency and lower production costs. This can include finishes such as:
- Bright Annealed: Heat treating steel in the right conditions creates a bright, reflective surface that can be buffed to make it more reflective.
- Cosmetic Brushed Finishes: A No. 4 brushed finish is bright but hides scuffs and fingerprints.
- Pre-Painted: Pre-painting adds a protective or decorative coating on a metal object.
- Pre-Plated: This alternative to plating coats the whole metal workpiece before the finishing cuts are made. This makes the treating process faster.
Cold Roll Forming vs. Hot Roll Forming
Roll forming operations can occur at (or slightly above) room temperature or significantly high temperatures. These two qualifications characterize the two types of roll forming available: cold roll forming and hot roll forming.
Cold forming involves making the shapes at, or slightly above, room temperature. Although the process does not require specialized material heating equipment, it does require more passes to shape the metal into the desired shape. Despite needing more time to complete a part or product (compared to hot forming), this method results in tighter tolerances and a higher quality end product. Additionally, cold rolled metal is often stronger than hot rolled metal because the additional passes harden and strengthen the material.
Hot forming is a metalworking process that combines the principles of extruding and rolling to shape molten steel under extremely high temperatures. Generally only used by steel mills and large-scale service centers, the process commonly creates structural materials such as those used to reinforce buildings. Compared to cold forming, hot forming is much more limited in application due to its higher investment costs, greater operator skill requirements, and smaller equipment capacities.
Custom Roll Forming Services at Premier Products
At Premier Products of Racine, we offer custom roll forming services. Our well-maintained, 210,000-square foot facility houses nine roll forming mills, which enables us to manufacture high-quality parts in thicknesses of .010–3/16 inches, up to 20 inches in width, and with virtually unlimited lengths. Our material capabilities range from aluminum and aluminized steel to stainless steel and titanium. To support our roll forming operations, we also offer finishing and in-process capabilities.
For more information about our roll forming services, contact us or request a quote today.
Case Studies
- Cosmetic Roll Forming of Stainless Steel Parts for the Appliance Industry
- Stainless Steel Fabrication of a Cosmetic Door Trim for the Consumer Appliance Industry
- Fabrication of Tube Burner for the Barbeque Industry
- Roll Formed Stainless Steel Tanker Truck Structural Beam
- Roll Formed Shelf Ladder for Appliance Industry